Pack integrity leak testing
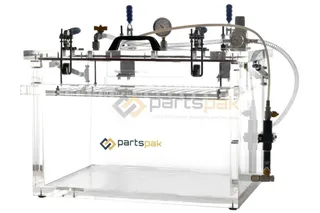
Is your pack reliably sealed?
Reliable sealed packs are critical to your product quality, prevent contamination, spills and ensure product integrity. Issues including packaging material variations, machine setup and seal area contamination are factors that can affect the packaging seal reliability.
Pack testing using a vacuum pack testing chamber, together with a controlled sampling procedure is critical to assuring your packed product remains safe and the high quality your customers expect.
A common method of package testing, often referred to as a bubble test or immersion leak test (Standard test ASTM D 3078-02), utilises clear vacuum chambers such as our acrylic chambers and submerges the package under water. As a vacuum is created, air inside the package can flow through any existing leaks in the packaging resulting in a trail of air bubbles rising to the top of the vacuum chamber. The air bubbles therefore give both a visual confirmation of a leak as well as the location of the leak, so you can begin your procedure to rectify the cause of the leak.
PartsPak vacuum pack testing chambers are available as rectangular (for larger packs and horizontal viewing) or cylindrical (for smaller and more vertical viewing). PartsPak design and manufacture to match your application requirements. Each chamber is supplied with all the necessary vacuum control and optional vacuum pump/venturi devices enabling simple plug and play operation. Testing chambers comply with ASTM D 3078-02 - Standard Test Method for Determination of Leaks in Flexible Packaging by Bubble Emission.
Find out about our range of rectangular and cylindrical pack testing chambers by downloading our brochure below:
Want to find out more? Contact us to discuss your requirements and ensure your packs are reliably sealed.